Blog
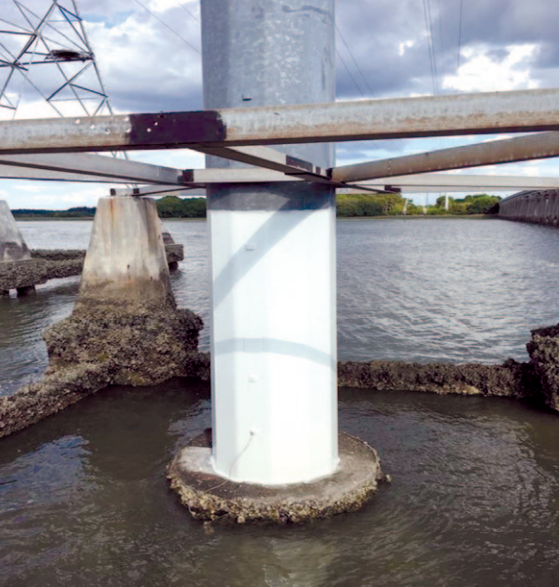
Corrocoat USA Successfully Battle Time and Tide
three years ago, Corrocoat usA was called in when a galvanised electricity transmission pole was found to be suffering from significant corrosion. the pole was situated in a tidal splash zone and was subject to continual exposure to seawater. On examination it was found that the sacrificial zinc lining around the base of the pole was already consumed and that the steel pole itself was corroding at an increasing rate. If left, the pole would suffer significant steel loss and would likely require expensive replacement. Corrocoat USA was asked to prepare and...
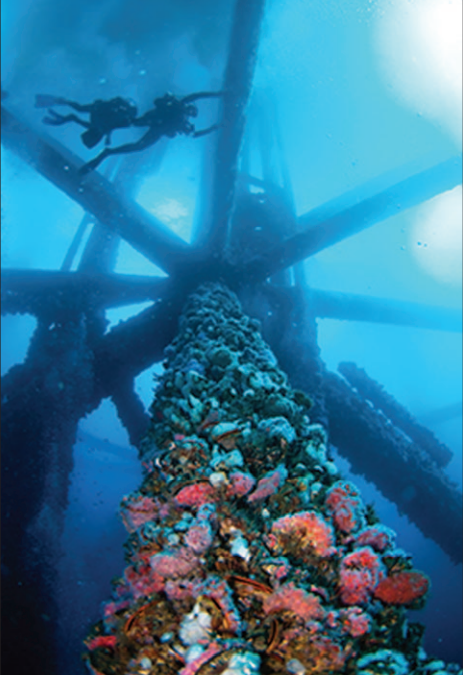
Underwater Coating system speeds up repair times and saves Down time
Corrocoat has launched an underwater repair system designed for use on submerged surfaces such as structural steelwork, pilings and jetties. based upon our well-established Plasmet range, the system is fresh and marine water tolerant and can be applied and cured whilst immersed. The system comprises: Plasmet UWP – an epoxy glass flake putty, Plasmet UWL – an epoxy laminate for application with glass fibre matting and Plasmet UWT – an epoxy glass flake topcoat. Plasmet UWP can be applied by trowel or by diver’s glove for localised repairs. After 24 hours the...
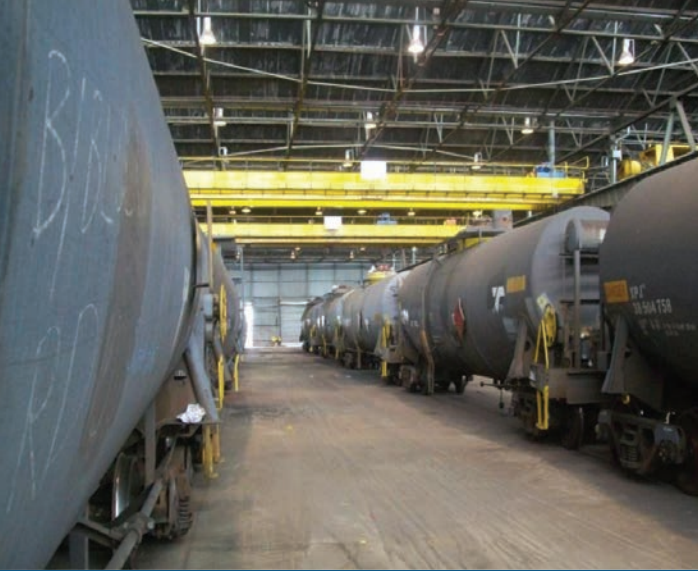
Ten yesrs on….still Going strong
ten years ago the whole of south Africa was busily preparing to host the football World Cup. Work on the stadia was on time but due to pipeline construction delays there were some concerns over supplies of aviation fuel being in the right place for the extra air travel generated. Transnet, Africa’s largest rail freight transporter, had a fleet of 400+ liquid rail tank wagons ready to take the job on but there was a problem. In order to carry aviation fuel the tanks first had to be protected against jet fuel and that’s when Corrocoat SA was consulted. Corrocoat...

Sweet smell of success
A vessel at a fragrance plant was used for mixing geranoil, acetic acid, and dosing with 50% naoh. the neutralisation of the 50% naoh in the process produces highly corrosive sodium acetate, a soluble salt which in just six years had effectively destroyed a previous epoxy coating and had begun to corrode the vessel itself. After required welding repairs were completed the entire tank was blast cleaned and then washed to remove soluble salts and then blasted again to a SSPC-SP10 quality. A holding primer was applied to the prepared surface prior to all pits being...
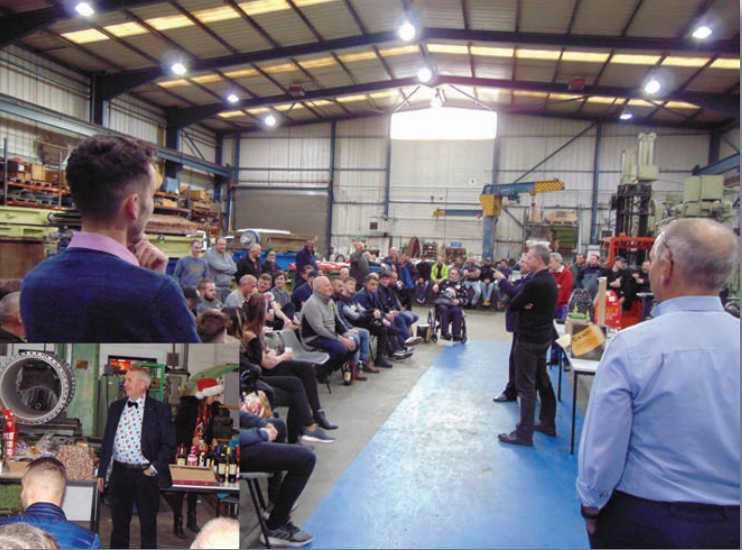
GOING, GOING, GONE!
In line with a tradition that stretches back decades, the staff at Corrocoat head office in leeds all got together on the last day before the Christmas break, for the annual grand auction. Each year a number of suppliers and contacts are kind enough to acknowledge with seasonal gifts their appreciation of the relationship with Corrocoat. It was decided many years ago that these gifts would be collected together and auctioned on the last day of business to the whole company. So, after a buffet lunch, laid on by the company, the whole team gathered in the...

Refurbishment and Corrosion Protection of a Cast Iron Condensate Pump Casing
Corrocoat’s Belarusian partner (Corrocoat AKZ) was recently commissioned to complete the refurbishment and corrosion protection of a cast iron condensate pump casing at a power station. the pump had been in operation for circa 10 years; pumping water at a temperature of 20-60°C with thermal spikes up to 70°C. on inspection it was found that the pump casing’s internal surface had suffered from cavitation and erosion wear. the depth of corrosion pits was in the range of 10-15 mm and the whole casing surface needed to be restored to original condition. The client...
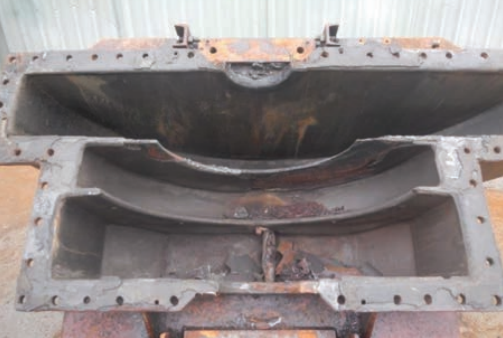
Well Blow me Down
vietnam Glo Coating engineering JsC (GCe) was required to refurbish, repair and coat a casing of an inert gas blower by plant operator Pvtrans oilfield services. the casing had in the past been coated with a rubber lining which would need to be completely removed as part of the work using uhP water jetting and hand tools where applicable. The internal surfaces were first abrasive blast cleaned to the required cleanliness level. A primer coat of 632 was applied initially followed by a build coat of 602-632 before the application of a final coat of Corroglass 652...
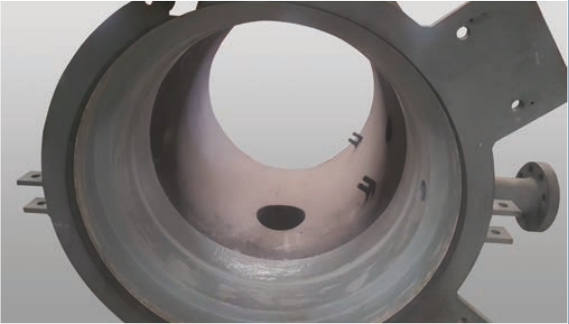
Protection Against Abrasion
In Qatar, Al huda Corrosion treatment was asked by Petrotech to inspect and recommend a coating system for internal corrosion protection of a hydrocyclone and its band lock. the hydrocyclone is used to separate two liquids of different densities, which in this case was oily water as well as sand creating an abrasive in-service environment. After inspection Al Huda recommended coating the cyclone with Plasmet HTE on the internal surface and door where heavy abrasion could be expected. Polyglass VEHA was used to rebuild the band lock closure areas to ensure the...
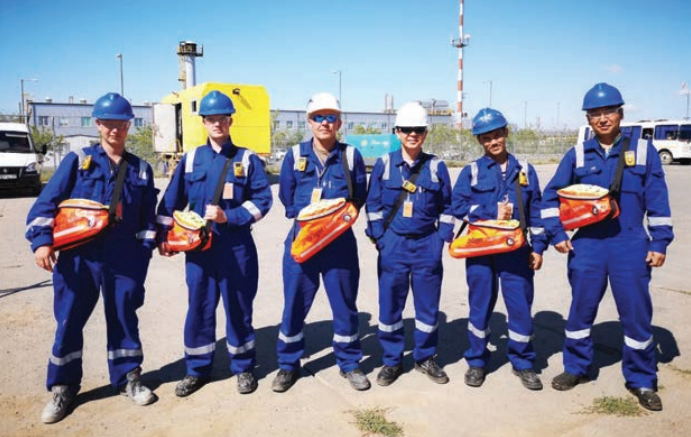
100 operatives…. 50 vessels…. 3 Weeks… 24/7? no Problem!
During september and october 2019 Corrocoat Caspian was appointed by KPo (Karachaganak Petroleum operating b.v.) as a key contractor for the lining of process vessels during a shutdown event which happens only once every five years. KPO b.v. is a consortium of international oil companies Royal Dutch Shell, Eni, Chevron, LUKOIL and KazMunaiGas who are developing the huge Karachaganak gas condensate field – one of the world’s largest. Located in northwest Kazakhstan it covers an area of over 280 square kilometres and holds an estimated gross reserve of over 2.4...
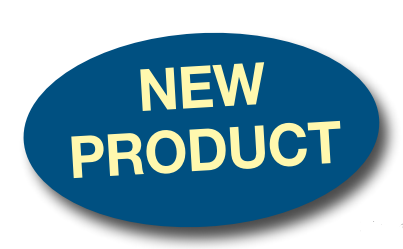
Corrocoat sel
Corrocoat SEL is a spray applied epoxy glassflake lining, intended for single or multi-coat application, that provides durable chemical protection in aggressive atmospheric conditions and immersed environments. Corrocoat SEL has a smooth finish and can withstand immersed temperature levels up to 90°C in oil, and non-immersed levels up to 100°C. It displays excellent resistance to discolouration that can occur on exposure to strong concentrations of acid. SEL has excellent application characteristics and edge coverage in single coats and is predominately applied...
Recent Comments